
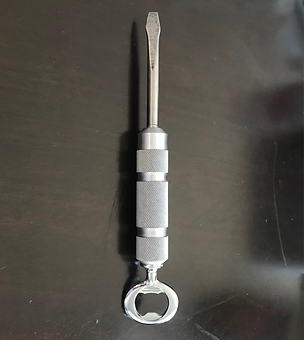
Screwdriver Project
For this project, I was tasked with creating a screw driver from a steel rod with a raw casted aluminum handle. This was done with a CNC lathe, to turn down and shape the handle, and manual lathe.
To go above and beyond, I chose to turn down the knuckling along the handle (clean bands in picture), anodize the handle (not pictured), and cut internal threads in the bottom which I secured a bottle opener in (seen to the left).

Lessons Learned
This was my third and final work piece in my Introduction to Manufacturing Processes class, so by the time I reach this project I knew my way around the machines necessary.
-
My first take away from this project was, being my third and final project in class, I felt the difference in both my confidence when machines, and my ability to quickly and affectively reach tolerances. This taught me that the more comfortable you can get with the machines you're operating, the more effectively you'll be able to use them.
-
The next lesson I learned from this project is to go slow along the way and if possible always check to make sure you're within tolerance, and/or the piece you are working on will mate correctly with its partner. With this project we had to make sure the screwdriver tip was within a certain tolerance, but also that it would fit into the head of the screw.
-
This lead to another lesson learned, which was that we had to put the main priority on function over sizing. In most operations these two should co-mingle, but this may not always be the case due to an engineer/ designer not understanding the necessary manufacturing processes, or may be caused for another unforeseen reason. However, It is always a good idea when start a project that will have a specific application to decide what needs to take priority and what can be left to the machinists best judgement.
-
-
The last and biggest take away I took from this project was to ALWAYS think ahead. Despite your knowledge on the entire process, try to visualize each step along the way. For example, on this project we started by cutting the handle out on the CNC, then put it on the lathe to knurl it, next you would forge the tip, grind the tip to shape, hear treat the tip, and finally finish. As seen in the picture at the top of this page I chose to put bands into the knurling for a more aesthetic look. The problem I ran into was that I had learned perviously to also perform finishing processes at the end, once all the processes that will most likely fail are complete. So, instead of getting rid of all the remaining aluminum the CNC hadn't gotten, and polishing the handle and bands, I went on to forging. The only problem with this is once the screwdriver is forged, the base becomes brittle, and cannot directly be put into the lathe without being secured in a non traditional way. This left me forced to hand sand and not properly finishing the screwdriver to the standard I had for it. So, the take away here is to always think ahead, not every process will be cut and dry, and some may require a complex and sometimes daunting procedure to design.

Cost Estimate
This estimate will take into account the price of the raw stock and the labor cost. (To view links of individual stock click on the size of each to be redirected.)
​
Raw Stock Cost:
Screwdriver Blank
Before I give the price I want to explain what the screwdriver blank was, and how that effected the price I got. To start, the blank was a steel rod, which had an aluminum handle casted onto it. So, to determine a price (Note: school priced them at $19.95) I will be try to calculate the worth of the individual materials.
​
Aluminum in Handle:
Rough Volume:
22.23 in^3 = 0.000364 m^3
Density of Aluminum:
27100 kg/m^3
Rough Mass Estimate:
9.87 kg
Current Price of Aluminum per kg:
$2.95
Price Based on Mass of Handle:
$29.12
​
Steel in Rod:
Rough Volume:
2.65 in^3 = 4.34*10^-5 m^3 = 0.0000434 m^3
Density of Steel:
7850kg/m^3
Rough Mass Estimate:
0.341 kg
Current Price of Steel per kg:
$0.28 (this was based on price $255 per 1 US ton)
Price Based on Mass of Rod:
$0.1
​
Estimated Material Cost:
$29.22
​
Labor Cost:
Colorado hourly wage of Machinist:
$18.53
Days spent (Rough estimate):
17
Rough average of hours per day:
2
Total Hours:
34
​
Total Labor Cost:
$630.02
Note: This was taken directly from the Clock time estimates as the total time I spent on both was roughly the same.
​
Total Project Cost:
$659.24
​
Notes:
My estimates price was 146% the price of the schools cost. I believe this disparagement is due to one of the follow: The price of aluminum had increased since the screw drivers were produced, since the amount of screw driver produced were so high, you school may had gotten a wholesale price, or my calculations were grossly inaccurate, which I don't believe is the case.

Improvements to be Made
When being asked how would I reduce the time and cost of this project, there is balance between the two. Automation along with CNC would reduce the time to produce this project, however the price of the necessary machinery may not be worth the decreased time. This has lead me to a process that I believe would both decrease time and money.
​
New Process
-
To begin, the process will be the same, the machinist will quickly secure the screw driver into the lathe, and use a center drill to create a hole for the dead center in the CNC lathe to sit in.
-
Next, the original process for this second step is to secure the screwdriver in the lathe (screwdriver tip inside jaws) and use a parallel of the specified size to make sure the lathe tool would have clearance to cut the top of the handle. The CNC had a preprogrammed code for us so it would run and we would grab you screwdriver and go. The step after would be knurling on a manual lathe, however I believe that we could mix these processes, along with the processes after knurling into one step. Here's how:​​
-
First, to ensure the drill rod had not been bent or damaged in any way, we will have a machinist perform an inspection on the straightness of the drill rod, if there is any bend or curve of any kind that screw driver blank will not be used.
-
Second, the machinist will quickly secure the screw driver into the lathe, and use a center drill to create a hole for the dead center in the CNC lathe to sit in.​​
-
Third, the pre-programmed code would have a new section where the lathe tool, instead of leaving the aluminum around the top of the handle, would face it off. This is the reason that we'll be having an inspection in the beginning. To understand this further look to the fifth point below for a visual.
-
Fourth, we would add a CNC knurling tool to the tool holder, this would happen before the code starts. since the CNC lathe knurling tool only relies on the height of the piece and the depth it has to be, after the screwdriver handle is faced and shaped, every single one will be in the same position. Being in the same position it's a simple addition to the code. Knurling, done.
-
Fifth, a stop would be added to the code, where the machinist would remove the tail-stock, slide the screwdriver rod up to the shoulder of the handle (max depth) in the jaws to decrease wobbling, and then restart the code. This last piece of code would face the remaining aluminum of the bottom of the handle (Note: Speed would be reduced for this part in the code).
-
To help me explain I will be referring to the image below, the red circled area are are the extra piece of aluminum that would remain from the current manufacturing process. These pieces would have to be removed with a manual lathe and belt sand after going to through the CNC, so I decided to expedite this process.
-
-
​
​
​
​
​
​
​
3. After the handle has been finished, forging must be done. I have been reluctant to use a robot, due to the cost,
however I believe that a articulating robot for the forging, sanding, heat treating, and finishing would greatly increase the speed of this project as well as the repeatability. With the advent of the articulating robot for this step, the operator would secure the screw driver installed into the arm of their robot or in a position when the robot has access to it. Next the die drop forging process would be the same, however the robot would replace the operator. Sensors would also be set up which measure the heat of the flame, and the screw driver, which would ensure a similar result between multiple screw drivers.
4. Next, the robot would use a circular saw which would be fixtured, making fro a solid and reliable environment, to cut the flash off of the screwdriver tip.
5. After, the robot would use a grinding surface to bring the tip to tolerance, and then to clean up the residue from heat treating.
6. Lastly, the robot would place the finished screwdriver to a designated surface, where the operator would collect it.
​​
Final Note:
This was a difficult process to speed up without increasing costs dramatically so I tried to keep all of the new processes within the currently available equipment at our lab.
​


Mass Production Estimate
I've been tasked to answer the question of how would the price compare if I made 10,000 of these screwdrivers vs the price of 10,000 screwdrivers manufactured through automation. To establish a baseline we'll first find the price of a machinist hand producing 10,000 screwdrivers.
​
Cost of 1 Machinist Produced Screwdriver:
$659.24
Time Spent on 1 Machinist Produced Screwdriver:
34 hours
Cost of 10,000 Machinist Produced Screwdriver:
$6,592,400
Time to Produce 10,000 Machinist Produced Screwdriver:
340,000 hours = 14167 days
​
Cost of 1 Automation Produced Screwdriver:
$29.22, this is the price for only the stocks, no labor cost.
Time Spent on 1 Automation Produced Screwdriver:
25-40 minutes, this was estimated using manufacturing time of similar size and complexity items, such as a water steel water bottle.
Cost of 10,000 Automation Produced Screwdriver:
$292,200
Time to Produce 10,000 Automation Produced Screwdriver:
5,000 hours = 208 days
​
Finals Notes:
This project was difficult to estimate the automated manufacturing time for 1 unit. There are so many details and processes in such a small part that it was difficult to find something to compare it to.
​